Technical Article
Published 04/2018
How much Testing is Enough?
Sharing Work Practices from Around the Globe
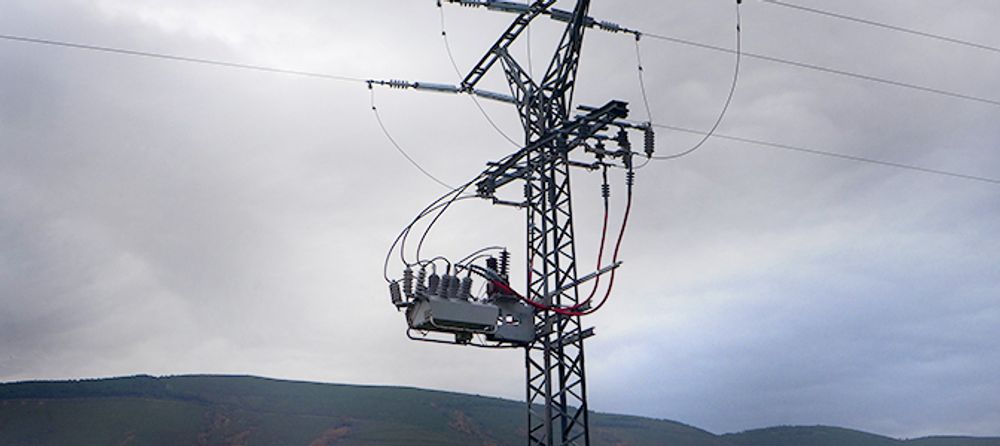
For electricity distribution utilities, testing the protection relays, switchgear and their communications is very much commonplace. Decades ago, utilities would procure from a multitude of vendors for their full system, before bringing it all together, constructing the project and testing the complete system. This was even the case for pole mounted switchgear, where Circuit Breakers, CTs and Control systems were purchased separately from different vendors, before being built and integrated onsite. Fast forward to the modern era, and the switchgear game has changed dramatically.
Firstly, with the advent of Microcontroller relays, and then the integration of sensors, control systems and SCADA Remote Terminal Units into a single product (such as any modern Automatic Circuit Recloser). In years gone by, complete end-to-end testing was warranted, as there was no guarantee that all the components would integrate correctly.
Today, when a utility purchases a fully integrated Recloser System, oftentimes the entire system has already been comprehensively tested at the factory. In fact, a lot of utilities are coming to realise that some of their classic testing regimes are unnecessary and expensive. In NOJA Power’s experience in 87 countries around the world with these ACR products, it’s certainly interesting to see who is leading the way with optimising the investment in testing and gaining the best reliability.
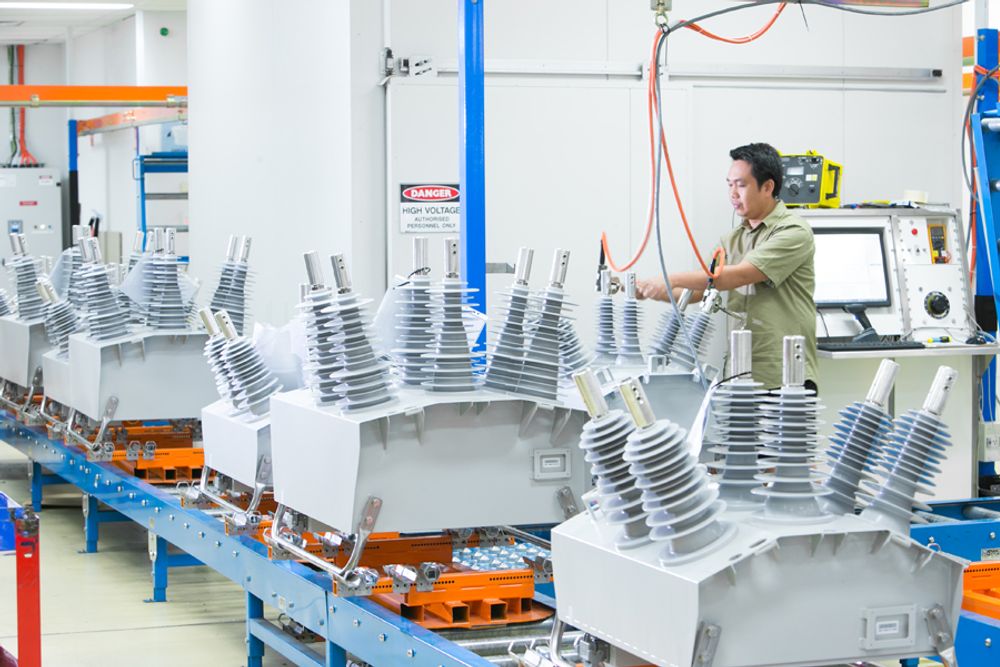
When a utility chooses to add a new product to its asset base, typically utilities will evaluate and test the prospective device. The issue today, is that commonly the scope of these tests is optimised around traditional systems, where each subcomponent (Sensors, Circuit Breaker, Relay, etc.) is procured separately. Now that all these components are purchased in one pre-tested package, a lot of investment can be saved by utilities in optimising their testing regime. Pragmatically, when a utility chooses to deploy these units, there are two distinct kinds of testing that unit is subject to:
- Acceptance Testing
- Routine Testing
Acceptance Testing is the process of verifying a system does what it claims to do. Typically, utilities will procure a single unit of the prospective product, and systematically evaluate all the functions that the utility wishes to use. This verification and acceptance testing is a valuable component of reliable network operation, as it demonstrates that the unit is capable of its claims, and utilities can be confident that they have performed their due diligence.
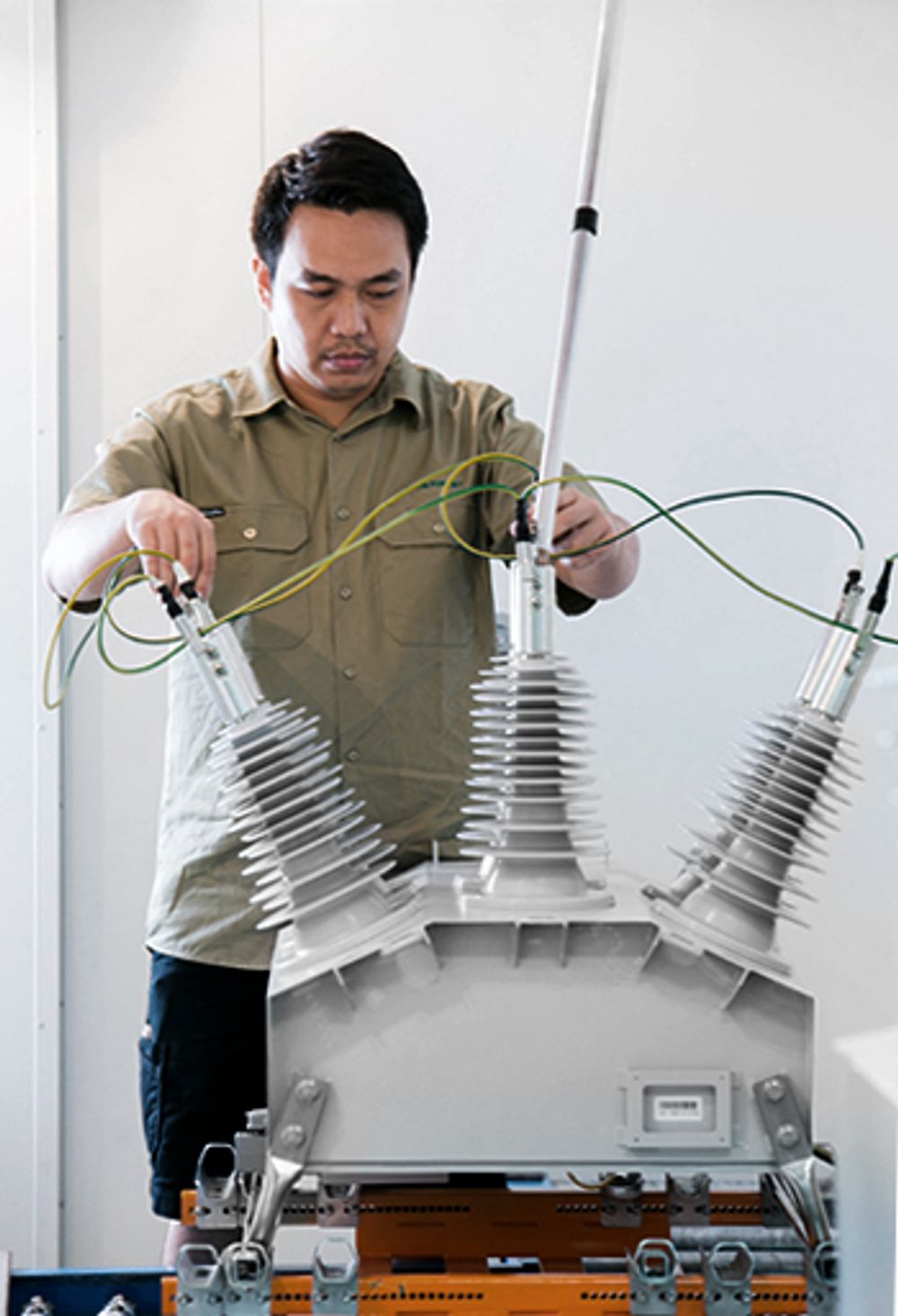
Routine testing is the process of checking every single unit that is procured, after a contract award. It is in this area that NOJA Power have witnessed the greatest divergence of work practices across the world. Whilst some utilities cling to the classic, highly expensive testing regime that would have been appropriate for non-integrated traditional systems, other utilities choose to rely on their acceptance testing for benchmarking and simply use routine testing as a sanity check.
The scope of routine testing seen in the field today varies greatly. Some utilities choose to test almost every protection point for response time. This can be a highly time consuming and expensive operation. The question remains though.
If:
- You have completed comprehensive Acceptance Testing
- You have checked all your functions work in the test device
- It’s a fully integrated system with a microprocessor control system
- The software and hardware versions are the same
Why would there be a reason to suspect that the device will not perform in the field?
Especially since most protection settings today are approved by a senior engineer before field deployment, and settings deployment to a field recloser can be as simple as a database point comparison(1), rather than a full set of injection tests.
And so, some utilities that choose to standardise on a firmware and hardware version feel sufficiently confident to proceed with an installation with only a few sanity checks. Utilities like these choose to forego the traditional protection point-to-point testing, as this has already been done at acceptance. All that they are interested in is verifying that the product has not been damaged in transit. A simple impedance check, perhaps a voltage injection and a cursory check that the sensors are picking up readings. These utilities are relying on the fact that every single NOJA Power OSM Recloser is comprehensively tested at the factory, with the signed test certificate supplied in the door pocket of the control cubicle.
“Every ACR manufactured by NOJA Power is 100% routine tested during the production process,” says NOJA Power Group Managing Director Neil O’Sullivan. “Customers can significantly reduce their operating costs by reducing the testing they need to do on receipt of the goods. We would recommend this testing is limited to confirm there has been no transport damage and the equipment is safe to energise and put into service. An insulation test, an impedance test and a reduced voltage power frequency test will confirm the equipment insulation system integrity. Microprocessor based controls have extensive self-checks built in and if the equipment powers up correctly and self-checks correctly then customers can have a high level of confidence the equipment is operating correctly and can be put in serviced safely. Validation of protection settings can normally be completed by either secondary or tertiary injection testing in a workshop environment or in the field. Remote control commissioning on site can be as simple as plugging in a SIM card today.”
The reality is, the utility best practice is best evaluated on an individual basis. If there is sufficient trust in the acceptance testing process, then utilities can stand to save a fortune in operational costs across a fleet of Automatic Circuit Reclosers. NOJA Power are aware that occasionally, commissioning costs are up to an order of magnitude more expensive than the product itself, and it is these utilities which stand to save the most from such refinement to the works practices. Ultimately, the most forward-thinking utilities evaluate the reasons why they do the testing, rather than simply following what has always been done before.
1 This is accomplished by programming the controller, then reading the settings state in the controller and comparing it with expected values. i.e. if the intention was for 50A Overcurrent pickup, an operator would scroll to the Overcurrent setting in the controller, and check that 50A was indeed the setting after the programming.
Want to stay up to date with Electrical Distribution Technology?
Join our list for a free weekly technical bulletin, as we share our Global Electrical Engineering experience directly to your inbox.
Subscribe →