Technical Article
Updated 03/2023
Using Automatic Battery Testing for Controlling Maintenance Intervals
Automatic Circuit Reclosers Application
"Maintenance Free” is a term which is often applied to modern distribution switchgear, but for any device that is destined for outdoor service life of 30 years, you will at least need to change a battery.
NOJA Power’s OSM Recloser system is no exception and the Maintenance Free principle applies, with the simple caveat of a periodic battery replacement in the UPS of the control cubicle. Whilst the costs of the battery itself may be small, the operational overhead expenditure of periodic maintenance can quickly add cost to the installation.
The 26Ah Lead Acid battery in a NOJA Power RC-10 or RC-15 controller will last typically as long as a car battery would in the same climate, but for many reasons (such as environment, quality, production variability) the real replacement time for a Lead Acid Battery varies widely.
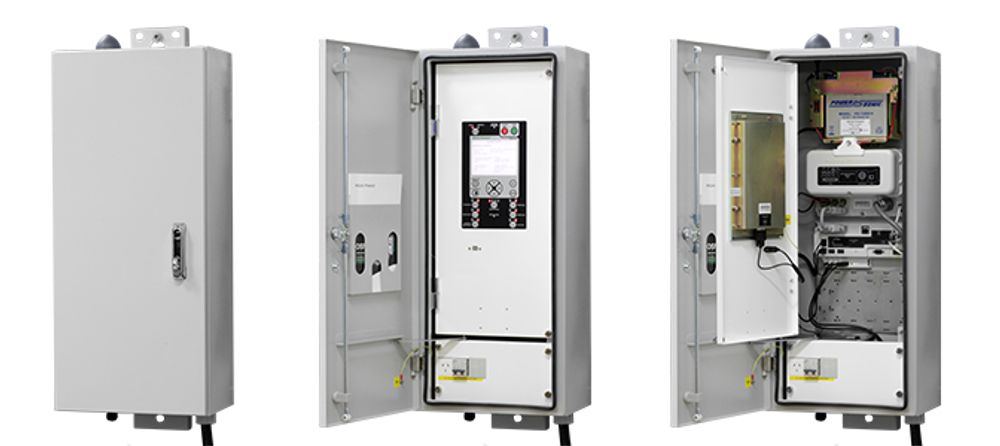
To catch all failures, oftentimes utilities employ a maintenance schedule that is short enough to catch each battery before it fails. In some places, this maintenance period is as short as 18 months. Whilst some environments may cause such premature aging, the reality is most of these units would still have some service life left in them.
Battery health is best assessed through a load test, rather than a time interval. As the only reason for a maintenance trip to Recloser installation, the efficiency gain of booking a maintenance team only when batteries are truly ready for replacement could save a utility thousands in operational costs.
NOJA Power’s OSM Recloser system has a built-in capability to run a periodic Automatic Battery Load test. This test automatically applies a resistive load across the terminals within the control cubicle and assesses the batteries’ capability to maintain voltage under load. If the battery passes the test, a “battery healthy” flag is set within the device. If it fails, a “Check Battery” flag is asserted, which can be reported remotely through existing SCADA channels.
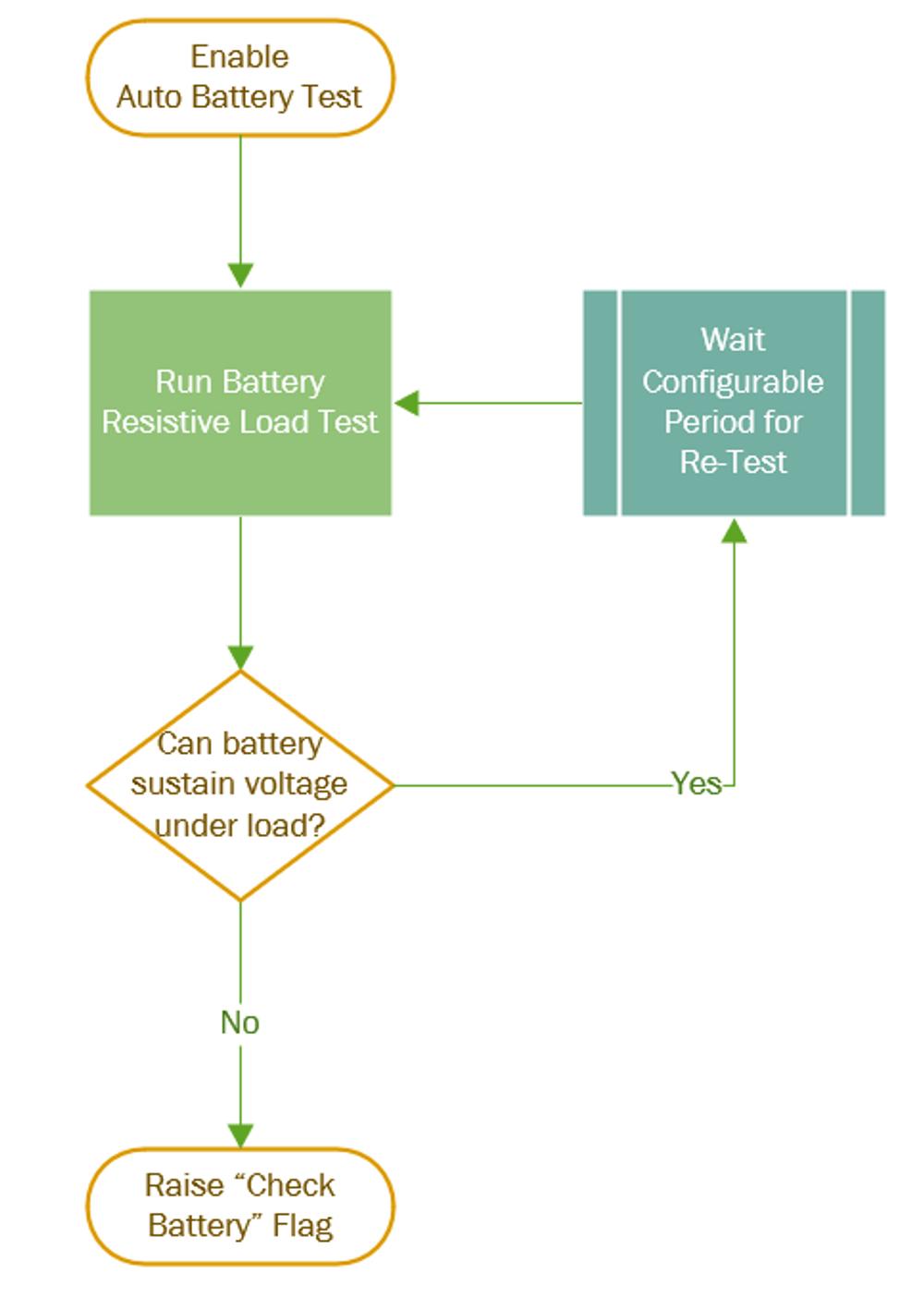
The Auto-Battery Test can be set to run periodically, such as once every 30 days. Protection and Control functionality is not compromised during the test, providing users with peace-of-mind during operation.
“Our battery systems are designed to have a replacement interval of five years at 20 degrees C operating temperature,” reports NOJA Power Group Managing Director Neil O’Sullivan. “Battery life is inversely proportional to temperature. The higher the average operating temperature the shorter the life of the battery. Reliability is best achieved by understanding what the realistic life of batteries are in the climate in which they are operating and implementing a battery replacement program within this period.”
By simply dispatching maintenance teams when the Recloser flags its battery requires replacement, utilities can gain the maximum performance from their battery asset and reduce the cost overheads of operating their fleet of OSM Reclosers.
Want to stay up to date with Electrical Distribution Technology?
Join our list for a free weekly technical bulletin, as we share our Global Electrical Engineering experience directly to your inbox.
Subscribe →