Technical Article
Published 04/2023
Achieving Electricity Network Reliability - An Interview with Neil O’Sullivan
Neil O’Sullivan knows electricity reliability. An engineering veteran of almost 40 years, Neil has worked in over 110 countries in improving distribution network reliability. A founding member, and the “N”, of NOJA Power, Neil’s experience has guided the development of power system reliability products.
In this interview, General Manager Marketing Martin van der Linde sat down with Neil O’Sullivan, with a goal to elucidate the key factors in achieving power system reliability.
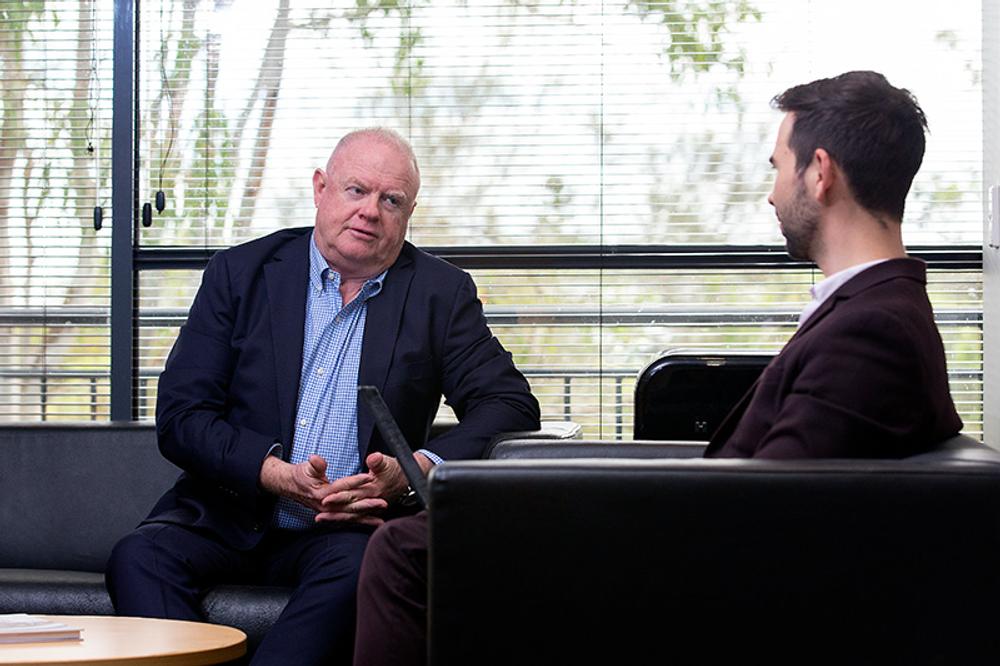
Martin: “Neil, when talking about power system reliability, what is your guiding view?”
Neil: “In my experience, reliability is a partnership achieved by high quality products, and high-quality installations. The quality of the installation is just as important as the product supplied. Aside from our investments in developing high reliability products, through materials selection and rigorous design and testing, we invest heavily in training our users on installation and operation so they can enjoy the reliability of their investment over 30 years or more.
Martin: “You mention materials selection, in the recloser context, what do you mean by this?”
Neil: “We make our product from the highest quality material. For example, we use either 304 or 316 grade marine stainless steel. We use high quality epoxy and silicone rubbers. Our electronics are military specification. We’ve made almost 100,000 Reclosers in 21 years, and over that time we’ve tested all materials to failure to offer only the best. However, all of this is only half of the reliability equation.”
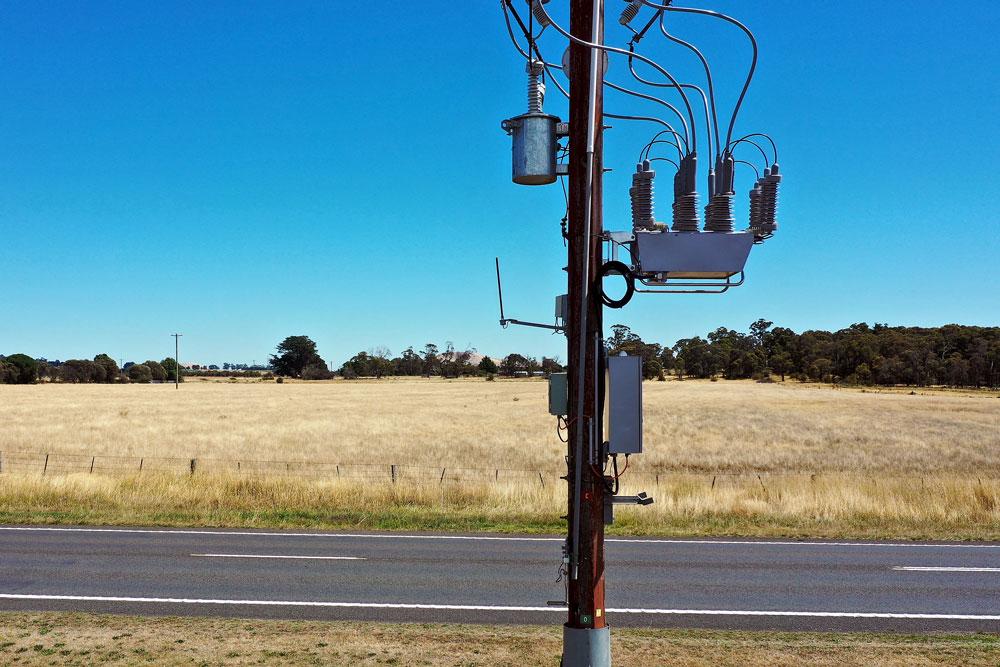
Martin: “OK, so what are the characteristics of a high quality installation?”
Neil: “Firstly, we take great attention to clearly describe this in our product documentation. We share instructional videos of high quality installations and conduct training for our users. The key requirements are earthing and correct programming.
Earthing is fundamentally important, as the equipment consists of both medium and low voltage components. Our first consideration is operator safety – we must be sure that any touch points are earthed. From a reliability perspective however, overhead lines are subject to regular surges, over-voltages and lightning. Our products are designed to handle this, proven by the type testing protocols we apply.
However, the earthing link between the primary switchgear, the controller, and the ground, ensures that the voltage potential moves equally between the devices. That is, if the voltage on the tank rises, so too does the controller and earth beneath it, meaning the potential difference does not exceed the rated specification.
It is this bond that ensures the product stays in specification and offers reliability.
Secondly, the material used for earthing needs to have a low impedance to high frequency events. Impulse events are not gradual changes in voltage, they are a step change. This is effectively a high frequency voltage. Materials such as steel offer low impedance at system frequency, but when the frequency goes up, so does their impedance.
The only acceptable materials that have this capability are copper, which we specify a minimum of 35mm2 conductor, or some copper coated steels with equivalent impedance.”
Martin: “So copper and copper coat are the only options?”
Neil: “Yes. And the copper coat must be equivalent in performance to a 35mm2 copper conductor.”
Martin: “Clear. You also mentioned programming, what is your advice in getting reliability here?”
Neil: “Again this comes down to fundamentals. Raising your substation breaker time to the short time limit, and grading simple overcurrent and earth fault protection in the reclosers down the feeder will offer the majority of your reliability improvements. After this is working, the progression to more complex protection can be added. There is not much point agonising over the details of admittance protection, or advanced Smart Grid Automation, if the reliability fundamentals aren’t in place.
We make all protection features that could be used in the distribution network available in the recloser product, but my recommendation is to get the fundamentals working first, then progressively add the other capabilities to handle the edge cases.”
Martin: “Lastly Neil, what is your advice to engineers starting to use Reclosers?”
Neil: “90% of faults on overhead networks are cured by opening and closing the auto recloser. So, you instantly get a 90% reliability improvement by making sure you correctly service grade the overcurrent and earth fault protection. The balance 10% reliability gain can be achieved with remote control and implementing more advanced protection or automation functionality, but the big gain is to simply install the recloser well, program it for auto reclosing and get that 90% reliability gain.”
Want to stay up to date with Electrical Distribution Technology?
Join our list for a free weekly technical bulletin, as we share our Global Electrical Engineering experience directly to your inbox.
Subscribe →